 |
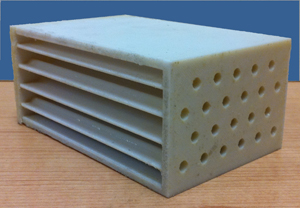
|
 |
Webbed tube heat exchanger |
|
The Clark School and Stratasys, Inc., announce the successful design, fabrication, and test of a Webbed Tube Heat Exchanger (WTHX), believed to be the first plastic heat exchanger made by additive manufacturing. Fabricated at the Stratasys facility in Eden Prairie, Minn., the 3D-printed WTHX promises to expand the potential applications of polymer heat exchangers to small production volumes and cost-constrained systems.
The WTHX represents the first time that a plastic heat exchanger has been manufactured through Stratasys’ Fused Deposition Modeling (FDM®) technology and used to successfully transfer heat through a polymer structure from a hot gas to a cold liquid. Room air, heated to 120 °C was cooled by building water at 27 °C, transferring nearly 65W of heat in the 500 cm³ heat exchanger.
Juan Cevallos, a Ph.D. candidate and research assistant in the Thermal Management of Photonic and Electronic Systems (TherPES) Laboratory at the Clark School’s Department of Mechanical Engineering, was responsible for testing the WTHX. Under the direction of Professor Avram Bar-Cohen–along with Professors S. K. Gupta, David Bigio, and Hugh Bruck–Cevallos has been working in collaboration with the Petroleum Institute in Abu Dhabi to advance polymer heat exchanger technology for seawater cooling of liquified natural gas processes, among other applications. The relatively high tool and assembly costs of low-volume polymer molding production led Bar-Cohen’s research team to select an additive manufacturing technology that could build complex geometries in a single step. Stratasys’ FDM technology provides that capability while using some of the strongest and most heat-resistant thermoplastics found among additive manufacturing technologies.
The WTHX geometry consists of a stack of rectangular flat plates, each containing an array of tubes that span the length of the plate and are separated by short webs. The tubular array carries the water, while the air flows in the gaps between the rectangular webbed-tube plates. The diameter of the tubes is selected to reduce the power required to pump the liquid while creating a “bumpy” surface on the gas-side that enhances heat transfer between the gas and liquid streams. Moreover, most of the heat transfer occurs directly across the thickness of the WTHX tubes, minimizing the deleterious effect of the low thermal conductivity of the polycarbonate resin.
Related Articles:
Alumna Appointed Director Arizona State University Polytechnic School NSF Grants for Graphene Research Awarded to Hu, Rubloff Avram Bar-Cohen to Step Down as ME Chair How Your Cell Phone Keeps Its Cool
January 23, 2012
|