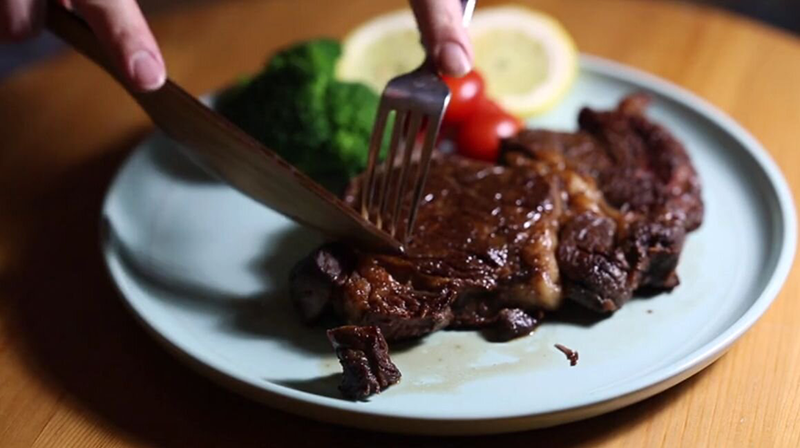
|
 |
Wood processed to be ultra-hard using a technique developed at UMD can be fashioned into a knife three times sharper than steel. Photo courtesy of Cell Press. |
|
Whether for building a house or a campfire, sitting at the kitchen table, or laying down a jam on a classic Martin guitar, there’s no shortage of uses for wood—utterly predictable uses.
But don’t tell that to engineers at Maryland. They’ve been innovating wildly with the ultimate sustainable material, from exploring new possibilities for wood’s use as a renewable structural material to exploiting its microscopic nanostructures for a revolutionary type of battery that could enable the efficient and safe energy storage needed for tomorrow’s green technologies.
UMD researchers, who have made dozens of discoveries over the years, published three papers revealing surprising ways to use wood in three of the top science journals in just the last week:
Shape of (Wooden) Things to Come
The advantages of wood as a structural material are legion: renewable, lightweight, naturally durable and strong, and possessing a lower lifecycle cost than most other materials. A new advance from the lab of materials science and engineering Professor Liangbing Hu addresses one of its shortcomings—a lack of formability like metal, plastic or concrete—by making the formerly rigid substance moldable, bypassing the requirement to cut or carve complex shapes.
As reported Thursday in the journal Science (where it was the cover story), his research team used a “water-shock” process to accomplish the feat. First, it removed the material lignin, which lends rigidity to wood, and then evaporated water from the wood. The wood was then “shocked” by reintroducing water to re-swell it, resulting in a material that is easily folded and molded.
"The resulting 3D-molded wood is six times stronger than the starting wood and comparable to widely used lightweight materials like aluminum alloys," said Hu, director of the Center for Materials Innovation.
Along with UMD, collaborators included Yale University, Ohio State University, U.S. Forest Service, University of Bristol, University of North Texas, ETH Zurich, and the Center for Materials Innovation.
Sharper Than Steel
Hardwood can be processed to be harder still. The result is a wooden dinner table knife that’s three times as sharp as a comparable stainless steel utensil, or wooden nails tough enough to be driven with a hammer through several layers of wood, according to a study published Wednesday in the journal Cell.
"The knife cuts through a medium-well done steak easily, with similar performance to a dinner table knife," said mechanical engineering Keystone Professor Teng Li, the study’s senior author.
Li’s technique focuses on preserving cellulose—the main component of wood that has a higher strength-to-density ratio than ceramics, metals or plastics—while removing weaker substances like lignin, which acts as a binder. This leaves wood “squishy,” he said, remedied by a process involving heat and pressure.
A mineral oil coating prevents water damage, making the knife a washable and reusable alternative to throwaway utensils. The material also has potential for hardwood flooring or wherever else super-tough wood is needed, Li said.
Better Batteries on Paper
A part of wood too small to see individually with the naked eye—tiny thread-like tubes known as cellulose nanofibrils that are an important component of paper—could help clear the way for solid-state batteries, which use solid rather than liquid electrolyte solutions, resulting in higher energy density and much greater safety.
Hu’s team soaked the fibers in a copper-alkaline solution, then inserted lithium ions into the material by bathing it in an electrolyte. The result is an efficient ion conductor that can easily be scaled up or down to suit energy storage needs, and without the risk of fire or explosion like conventional lithium-ion batteries. Batteries using the material are inexpensive, easy to assemble and eco-friendly.
The advance was reported Wednesday in the journal Nature and was a collaborative effort of UMD, the U.S. Army Research Laboratory, University of Münster, University of Tokyo, CUNY, Florida State University, University of Delaware and National Institute of Standards and Technology.
This story originally appeared in Maryland Today.
October 25, 2021
|